Max Pollock was pleasantly surprised when he noticed increased demand for reclaimed wood during the pandemic. He is the director of Brick + Board, an enterprise which processes wood salvaged from deconstructed vacant homes. This reclaimed wood is pricier than new lumber, so when states imposed lockdowns, Pollock expected his consumer base to dry up.
“There was so much uncertainty about the fate of the economy that we thought people wouldn't be buying expensive wood,” Pollock said in an interview with The News-Letter. “But I think that the increased demand for lumber may have closed the price gap, if not fully, then by a lot.”
A combination of increased demand as more people renovate their homes and constricted supply exacerbated by harmful environmental conditions has markedly increased the price of lumber. It was reported last week that the price of a thousand board feet of lumber is approximately $1,300, much higher than the pre-pandemic price of $350 to $500.
Since price has become less of a differentiating factor, it seems that more consumers are opting for wood that offers not only a unique aesthetic, but also positive environmental and social impacts.
‘A Coalition of the Willing’
The story of Brick + Board began in 2012 with the Baltimore Wood Project and the idea that wood collected from deconstructed abandoned buildings, or fresh-cut wood from felled or fallen trees in Baltimore, can be reused rather than dumped in a landfill.
Research from the U.S. Forest Service indicated that in some years, more wood was generated from urban areas than was harvested from national forests. Baltimore City, according to data from the National Renewable Energy Lab (NREL), generated approximately 76,000 tons of urban wood waste.
In an interview with The News-Letter, Morgan Grove, a research scientist and team leader for the United States Department of Agriculture (USDA) Forest Service Baltimore Field Station, described the many intricacies of the Baltimore Wood Project.
“In complex systems, you have lots of parts, but you also have feedback loops that are positive or negative and you have emergent qualities in the interactions among the parts that are not predictable,” Grove said.
It’s a complex system because the Baltimore Wood Project was not founded simply for reusing wood. It created jobs for people with barriers to employment and began to tackle the blight of abandoned houses. Working toward addressing those problems required a partnership between the Baltimore City government, the nonprofit Humanim, the USDA Forest Service and a host of governmental, private and nonprofit entities.
Estimates suggest that there are 16,000 vacant houses in Baltimore City, although the true number may be as high as 40,000. Mike Galvin, the director of SavATree Consulting Group, told The News-Letter that the partners involved in the Baltimore Wood Project first needed to evaluate if deconstruction would yield materials that, when sold, would offset the costs of the program.
“So the first question for us was, ‘Does it make any sense to deconstruct buildings rather than demolish them? Is there any value?’” Galvin said.
An analysis by scientists in the Baltimore Field Station helped to discover that the wood used to construct most of the abandoned row houses were harvested from southern yellow pine forests. The wood was “old-growth” — taken from trees that were 300 to 500 years old when they were harvested. This wood is invaluable, according to Galvin.
“The yellow pine material has virtually all been cut over; it hardly exists anymore in nature. The only place we can find it is by pulling it out of these buildings,” Galvin said.
There were also environmental benefits. According to data from Climate Matters, carbon dioxide emissions generated by human activity in the past several decades are unrivaled. Carbon dioxide, a greenhouse gas, traps heat in the atmosphere and its levels of emissions closely track with global temperatures. When reclaimed wood is converted into furniture, flooring or trimwork, carbon remains stored in the wood.
Jeff Carroll, the director of a division of Humanim called Details Deconstruction, highlighted the long term benefits of using reclaimed wood in an interview with The News-Letter.
“When the wood from demolished houses are cut into firewood or taken to a landfill, all of that carbon that was captured in that tree is going to be lost. It's going to go back into the atmosphere,“ Carroll said. “We want to capture it in durable goods so that it stays sequestered for another 100 years.”
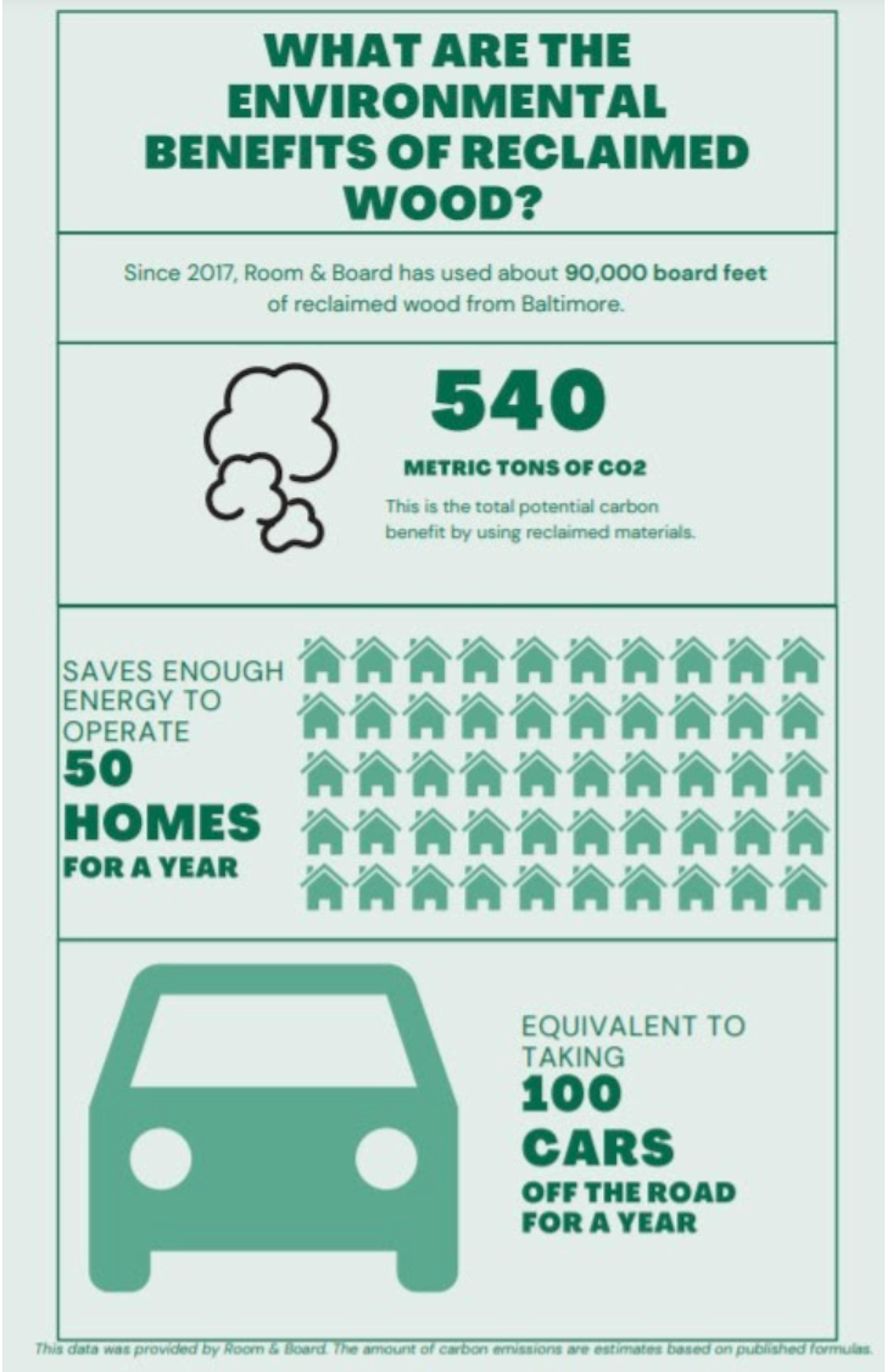
COURTESY OF TRISHA PARAYIL
The estimated environmental benefits of using reclaimed wood based on data provided by Room & Board.
Carroll’s expertise was critical throughout the duration of the Baltimore Wood Project. Carroll entered the deconstruction field in 2008, when the economic downturn compelled him to expand his role as a commercial contractor. He was drawn to the deconstruction sector and founded Details Deconstruction in 2012.
Two years later, in 2014, Details Deconstruction was selected by the Baltimore City government to lead the first deconstruction pilot of abandoned homes in the city.
When the pilot began, Carroll hired Pollock to oversee the sales of the wood material that was salvaged. Eventually, the sales department of Details Deconstruction became its own enterprise — called Brick + Board — led by Pollock. In the two years of the pilot, the company deconstructed 100 houses. Then from 2016 to 2020, the operation expanded to a deconstruction rate of about 200 houses per year.
Compared to demolition, deconstructing an abandoned home is estimated to create six to eight more jobs. Of the approximately 200 people who were a part of the workforce of Details Deconstruction, about 75% were previously incarcerated, according to Carroll. Hiring individuals with a history of incarceration was a priority for the enterprise.
“We wanted to employ people who did not have a ramp to enter the ‘employment highway.’ The best way to build the ‘on-ramp’ is to build an enterprise that was designed from day one to be an employment vehicle for those individuals,” Carroll said. “Deconstruction is labor-intensive work — there was a low barrier of entry to get in. A person could come in with minimal skills and then gain quite a bit of skills while they were working.”
An evaluation of the Baltimore Wood Project estimated that the recidivism rate for people employed through Details Deconstruction is about 25%, which is half the estimated recidivism rate for the city.
‘A Proof of Concept’
By the time the contract between Details Deconstruction and the Baltimore City government expired in 2020, wood and bricks from approximately 800 houses had been salvaged. The expiration of the contract coincided with rising COVID-19 infections, so the renewal of the contract was put on hiatus in March 2020 and has yet to be renewed.
Pollock saw potential in moving Brick + Board to the private sector, so he bought the enterprise from Humanim and converted it to a for-profit company.
“It's proof of concept that you can take something that was incubated in a nonprofit setting and with foundational funding, you can get it to a place where it can stand on its own two feet,” Pollock said. “I think it's a success story.”
Since 2012, Brick + Board has produced about 1.5 million board feet, of which approximately 70% is reclaimed wood, Pollock said. The company currently has partnerships with furniture makers in the Mid-Atlantic region. One of its biggest partners is Room & Board, a furniture manufacturer based in Minneapolis.
Since 2017, when Room & Board partnered with Brick + Board, Room & Board has used about 90,000 board feet of reclaimed wood from Baltimore. Based on estimates by Room & Board, 154 metric tons of carbon dioxide are stored in that many board feet and about 326 metric tons of carbon dioxide emissions were avoided by using reclaimed wood. The total potential carbon benefit of using reclaimed materials — 480 metric tons of carbon dioxide — is the equivalent of taking 100 cars off the road for a year.
According to Gene Wilson, the director of merchandising and vendor management at Room & Board, there are 11 collections of products created from urban wood in Baltimore, with over 8,500 products sold to customers since January 2018. He hopes that other cities will create a similarly robust urban wood economy.
“What's happened in Baltimore is just to hopefully inspire other municipalities to do something a little bit different than what they have done historically,” Wilson said. “And that is really taking wood from the waste stream and turning it into something of value, storing the carbon and having a positive impact on the environment.”